Understanding the Secret Components and Repair Service Strategies for Product Packaging Machine Maintenance
Effective upkeep of product packaging makers pivots on an extensive understanding of their essential elements, including the framework, drive system, and securing systems. Identifying common maintenance concerns, paired with the execution of preventative approaches and troubleshooting methods, can dramatically enhance device reliability.
Key Elements of Product Packaging Makers
Product packaging machines are composed of numerous crucial elements that interact to make certain efficient and efficient product packaging procedures. At the core of these devices is the framework, which supplies structural integrity and houses the numerous operating components. The drive system, typically a mix of motors and equipments, promotes the motion of elements, enabling specific operation throughout the packaging cycle.
An additional vital component is the conveyor system, which transports products with various stages of the packaging procedure. This is frequently matched by sensing units and controls that keep an eye on the setting and speed of items, making certain synchronization and lessening errors. The filling system is crucial for accurately dispensing the best quantity of product into plans, whether in fluid, powder, or solid kind.
Sealing devices, including warmth sealers or adhesive applicators, play an important duty in safeguarding plans, protecting against contamination and prolonging life span. Furthermore, classifying systems are indispensable for giving essential product information, guaranteeing compliance with guidelines. Ultimately, the control board, equipped with straightforward user interfaces, enables operators to manage machine features, display efficiency, and make adjustments as required, making certain ideal performance and efficiency in packaging procedures.
Usual Maintenance Problems
Reliable procedure of product packaging devices depends heavily on regular maintenance to prevent usual problems that can interfere with production. Among these issues, mechanical wear and tear is prevalent, especially in parts like conveyors, seals, and motors, which can lead to unforeseen downtimes. Additionally, misalignment of components can result in ineffective procedure, triggering items to be incorrectly packaged or harmed throughout the process.
One more common upkeep issue involves the build-up of dirt and debris, which can disrupt the machine's sensing units and moving components. packaging machine repair service. This not just influences efficiency yet can likewise present safety dangers. Lubrication failings can lead to enhanced friction, resulting in getting too hot and ultimate element failure.
Electric problems, often originating from loosened links or worn-out wiring, can disrupt machinery functions, leading to substantial production delays. Software program problems due to outdated programs or inappropriate setups can hinder the equipment's procedure, necessitating immediate intervention. Attending to these typical maintenance concerns proactively is necessary for guaranteeing optimum performance and durability of packaging equipment.
Preventative Upkeep Approaches
Executing preventative upkeep techniques is crucial for sustaining the effectiveness and reliability of packaging devices. These methods include a methodical strategy to maintenance, concentrating on the routine examination and maintenance of tools to preempt possible failings. By sticking to an arranged upkeep program, operators can recognize damage on elements before they lead to considerable failures.
Crucial element of a preventative upkeep strategy include routine examinations, cleaning, element, and lubrication replacements based upon supplier recommendations. Utilizing checklists can enhance this procedure, ensuring that no important tasks are ignored. In addition, maintaining precise records of maintenance tasks help in tracking the equipment's efficiency with time, facilitating informed decision-making concerning future maintenance requirements.
Training personnel on the significance of preventative maintenance boosts compliance and promotes a culture of proactive care. Executing a official statement predictive maintenance component, utilizing data analytics and sensor technology, can further optimize machinery efficiency by anticipating failures prior to they take place.
Troubleshooting Techniques
When confronted with malfunctions or ineffectiveness in product packaging machines, employing methodical troubleshooting strategies is crucial for determining and solving problems swiftly. The initial action in effective troubleshooting is to develop a clear understanding of the device's functional parameters and efficiency metrics. This involves assessing the device's requirements, as well as any kind of mistake codes or signals displayed.
Next, operators ought to conduct an aesthetic assessment, checking for noticeable indicators of misalignment, wear, or damages. This often consists of analyzing belts, gears, and sensors to pinpoint prospective causes of breakdown. Gathering functional information, such as manufacturing rates and downtime logs, can likewise provide understandings into persisting problems.
Once prospective problems are determined, using a rational approach to isolate the origin reason is essential. This might require screening specific elements or systems in a regulated way. Participating in discussions with drivers who engage with the equipment on a regular basis can generate useful feedback regarding uncommon habits or patterns.

Repair Work and Substitute Best Practices
A thorough understanding of repair and replacement ideal techniques is essential for preserving the durability and performance of packaging machines. Routinely examining the problem of device components enables timely intervention, preventing more considerable issues that can result in pricey downtimes.
When repair work are needed, it is important to make use of OEM (Original Equipment Maker) parts to make sure compatibility and efficiency. This not just maintains the honesty of the device yet likewise maintains service warranty arrangements. Furthermore, it is suggested to preserve an inventory of important spare parts to facilitate quick substitutes and decrease functional interruptions.
For complicated repairs, engaging qualified technicians with specialized training in product packaging equipment is advised. They have the experience to detect problems precisely and perform repair work efficiently. Recording all repair service activities and parts substitutes is important for preserving a comprehensive maintenance history, which can help in future troubleshooting.
Last but not least, executing an aggressive technique, including normal evaluations and predictive maintenance techniques, enhances the check my reference integrity of packaging machines. By sticking to these ideal methods, services can guarantee optimum maker performance, minimize operational dangers, and extend equipment life-span.
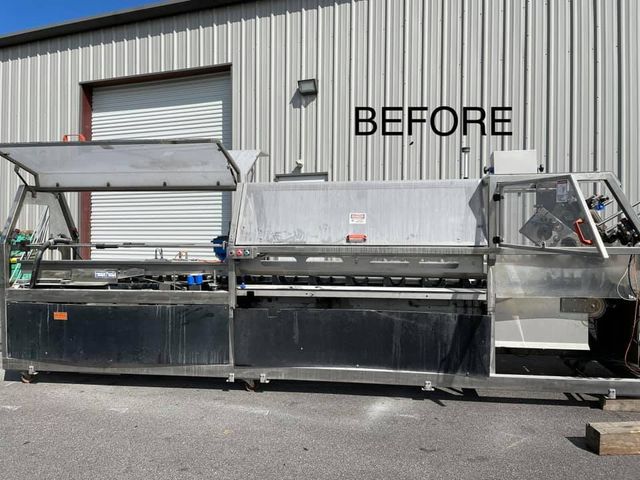
Conclusion
In verdict, a thorough understanding of product packaging equipment components and reliable maintenance strategies is vital for optimal efficiency. Regular assessments and using OEM parts can substantially reduce downtime, while a well-documented maintenance history promotes positive treatment. Using qualified professionals even more enhances repair work top quality and reliability. By executing these techniques, companies can ensure the durability and performance of product packaging machines, inevitably adding to improved operational efficiency and decreased expenses.
Effective upkeep of packaging makers pivots on a complete understanding of their essential elements, including the framework, drive system, and sealing systems.Effective procedure of explanation product packaging makers depends heavily on regular maintenance to protect against usual concerns that can interfere with production.Implementing preventative upkeep techniques is essential for sustaining the efficiency and integrity of product packaging makers. Furthermore, maintaining exact documents of upkeep tasks aids in tracking the machine's efficiency over time, facilitating notified decision-making concerning future maintenance requirements.
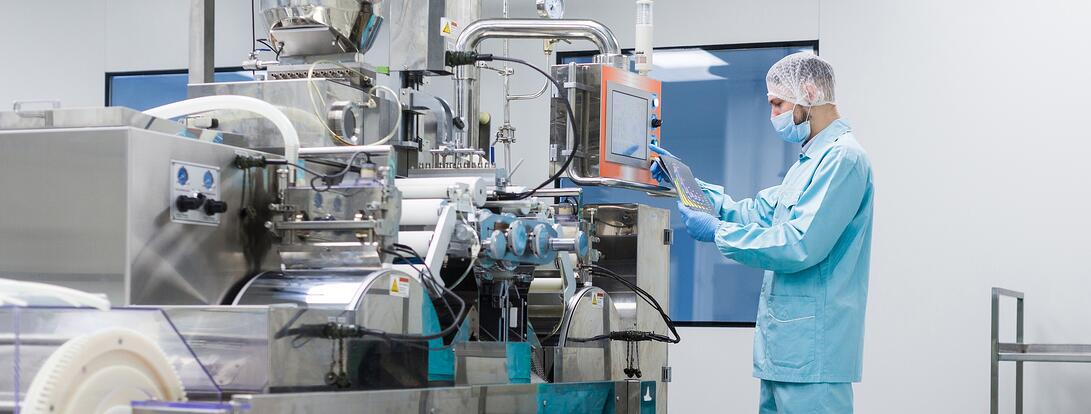
Comments on “Top Notch Packaging Machine Repair Service to Enhance Production Efficiency”